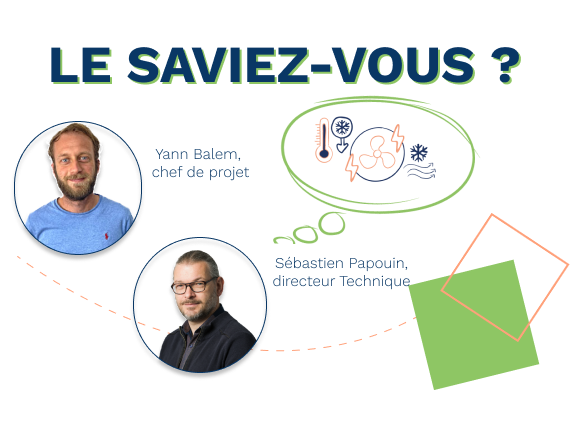
Optimizing Industrial Refrigeration: How to Control this Energy-Intensive Area?
Agri-food, cosmetics, pharmaceuticals… In several sectors, the industrial cold center is as crucial as it is expensive. Dametis provides solutions to reduce costs while increasing the performance of the industrial production process.
Our experts, Sébastien Papouin, technical director and Yann Balem, project manager, tell you about this energy-intensive hub
Industrial Refrigeration, What Is It?
Air conditioning, product freezing, low-temperature storage… Refrigeration is an industrial process used in all sectors.
“Cooling a closed space involves removing heat to reject it outside,” summarizes Sébastien Papouin, technical energy director at Dametis, during a technical training session at the Dametis Academy. “This results in a decrease in temperature.” For this, a thermodynamic system consisting of several elements is used: a compressor, an expansion valve, a condenser, and an evaporator. The latter two are heat exchangers. Industrial refrigeration occurs when the evaporator cools the building, and high-temperature heat pump occurs when the condenser heats the building. This installation can be present in the form of an outdoor unit or a machine room indoors. This industrial refrigeration area, so common in industry, is also one of the most energy-intensive.
“Refrigeration production can account for up to 60% of a site’s electricity consumption in certain sectors” reminds the Agency for Ecological Transition (ADEME), in its guideEnergy Management in Industrial Refrigeration,published in 2017. The rise in energy prices since 2022 and climate change accentuate this share. However, concrete solutions can be provided to reduce the bill and help optimize industrial refrigeration.
Some Best Practices for Managing Industrial Refrigeration
To reduce energy consumption, it is imperative to adopt certain best practices. The components of a refrigeration machine are calibrated for specific temperatures and pressures. Therefore, the control of the installation is essential. For example, in a system controlled by fixed setpoints, it is possible that it consumes more than it should, explains Yann Balem. The control of such installations can be complex because to be optimized, the operator will have to regularly modify the setpoint. In practice, installations can be observed that change their setpoint every three months. Ideally, a dynamic setpoint system would automatically optimize the installation’s consumption.
Finally, for optimizing industrial refrigeration, maintenance must be regularly performed: cleaning condensers and checking thermal insulation, purging non-condensables, etc.
Optimization and Investment
The refrigeration cycle can be optimized. Several values must be observed for this: those of low and high pressure, as well as temperature differences at the condenser and evaporator levels. “The lower the low pressure, the more we consume,” recalls Sébastien Papouin. “Well adjusted, we can achieve a 2% optimization on compressors.”
Furthermore, to optimize industrial refrigeration, Dametis recommends using self-adaptive electronic expansion valves. This investment allows adjusting the refrigerant flow rate in the evaporator to perfectly match the refrigeration needs. Similarly, the implementation of variable speed drives on air condensers allows for Floating HP regulation, generating energy savings of up to 15%.
Another habit to adopt is the regulation of the distribution pumps for refrigerant fluids. “By controlling the pumps according to the needs, we save an average of 50% of the pump consumption,” adds Sébastien Papouin.
How and Why Recover Heat?
There are three main ways to recover heat rejected by a refrigeration system:
- The first is to recover heat from superheating at the compressor outlet. When the refrigerant is compressed by the compressor, its temperature increases significantly. The most often used technology is the implementation of a Gas/Water heat exchanger (called a Superheater), which allows heating water to high temperature (up to 70°C). The superheater allows recovering up to 10% of the total energy rejected by the refrigeration system.
- The second is to recover heat from the condensation of the refrigerant. The simplest way is to install a Gas/Water heat exchanger, which allows condensing the gas and heating water at medium temperature (from 30°C to 60°C depending on the characteristics of the refrigeration system). The advantage of the condenser is that up to 100% of the total energy rejected by the refrigeration system can be recovered.
- The last method is to recover heat from the compressor oil. Indeed, the compressor of a refrigeration system generates heat due to the friction and mechanical work involved in the compression process. This heat is usually dissipated by the compressor oil. Compressor oil heat recovery allows heating water to high temperature (up to 70°C). This technology is very interesting for screw compressors where we can recover up to 10% of the total power rejected by the refrigeration system.
This heat recovery can be used for a multitude of needs and can help reduce gas or electrical consumption in the factory. “The heat is first injected into the process needs: production of domestic hot water, heating of certain process elements, heating of boiler auxiliaries,” lists Sébastien. Afterward, it can be used to heat premises and, if there is excess, used for innovative processes such as cold or electricity production.
Heat recovery contributes to improving the overall energy efficiency of the refrigeration system by using heat that would otherwise be dissipated and therefore not valorized.
All these processes can reduce heating costs, improve installation performance, and strongly contribute to more sustainable environmental practices.
Up to 100% of the energy rejected by the refrigeration system can be recovered. The rejected power is equal to the sum of the cooling power and the electrical power of the compressors.
A comprehensive offer for a high-performance refrigeration installation with a low impact.
Dametis carries out projects ranging from design to final realization. Its experts can size the refrigeration installation according to the process needs to optimize your industrial refrigeration management. For example, Dametis accompanied alginate producers by installing a new refrigeration production where 100% of the heat is valorized in the process.
Then, Dametis takes care of setting up smart regulation to obtain constantly optimal operating setpoints for low-pressure, fan operation in the condenser, and distribution pumps.
These optimizations can be easily identified using the EMS MyDametis software. Additionally, the software automatically detects drifts to maintain performance over time.
Each solution is adapted to the specific issues of industries, with continuous improvement of performance and systematic cost reduction.