Energy Management to reduce your consumption and costs
Do you want to control your energy consumption and reduce costs? Energy Management is a crucial step in achieving your energy transition goals.
What is Energy Management?
Energy Management is a strategic approach focused on enhancing the energy performance of an organization or industrial site.
Las empresas e industrias hoy en día enfrentan importantes desafíos:
- Mantener su competitividad (especialmente en un contexto de inflación con volatilidad en los precios de la energía) mediante el control de sus costos.
- Reduce their environmental footprint (whether due to regulatory obligations or to meet consumer expectations) through the decarbonization of the company’s activities, including upstream (raw materials, suppliers, and logistics) and downstream (logistics, usage, and recycling) processes.
Implementing an Energy Management system at an industrial site fits perfectly within this dynamic: reducing energy consumption and limiting water usage, which leads to a reduction in the site’s CO2 emissions and a decrease in utility bills.
For industries, there are two approaches to Energy Management: at the production site level or at the industrial group level.
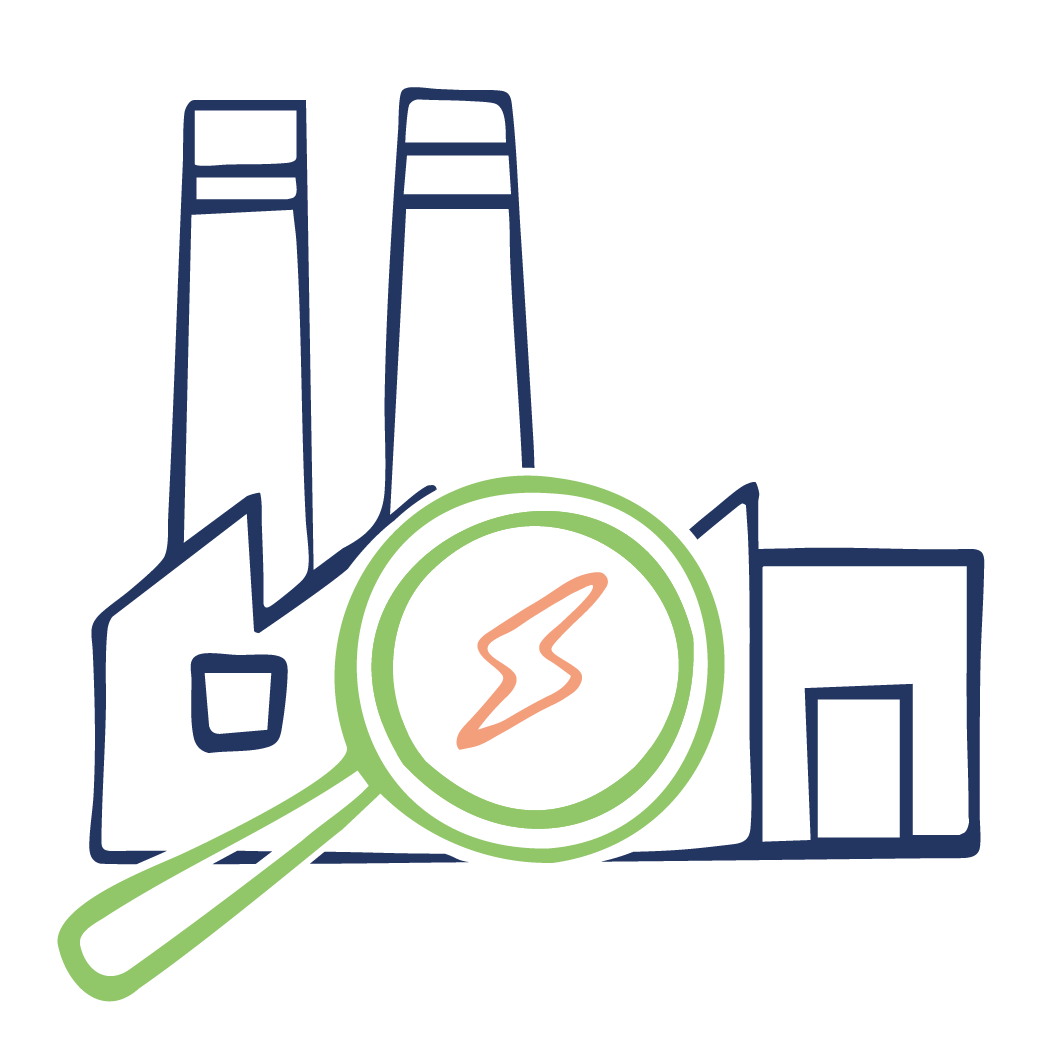
On-Site Energy Management
The implementation of Energy Management on-site presents an opportunity to understand, analyze, and optimize energy and water consumption across various industrial equipment. Here’s how the system is implemented in practice:
- Implementation of a standard energy monitoring system:
- Develop a Metering Plan to Determine Instrumentation Levels and Monitorable Energies:
- Map water and energy consumption, define energy uses and the associated performance indicators (IPE or KPI)
(Note: IPE should take influencing factors into account). - Create a routine for monitoring and analyzing IPEs to identify anomalies or deviations
- Conduct audits and other specific, one-time missions:
- Regulatory energy audit: This is a very basic audit that can be useful for mapping out energy consumption (~€7,000 for a medium-sized plant).
- Energy Audit: This type of audit is useful for analyzing in detail the energy utilities, understanding the link between utilities and processes, and initiating the development of a factory master plan (~€17,000 for a medium-sized plant).
- Detailed Audit: This type of audit is very thorough and is usually conducted within a specific scope. It is highly useful for structuring a future project.
- Measurement Plan: This is an assessment of the measurement instruments and other data sources that can be useful for tracking water and energy consumption. This type of mission also helps define the necessary measurement points to advance energy management.
- Carbon Footprint Assessment (Scope 1 2): Simplified analysis of CO2 emissions based on the plant’s energy consumption.
- Comprehensive Carbon Footprint (Scope 1, 2, and 3): A very detailed analysis that considers the entire value chain (upstream and downstream). It is often associated with a life cycle assessment (LCA).
- Energy supply contractualization:
- Energy supply contracts have a direct impact on costs and CO2 emissions. Therefore, it is important to define:
- the factory’s consumption profile and its evolution over the next three years.
- site strategy: decarbonized energy, fixed or variable pricing, etc.
- Establishment of contracts and ongoing negotiations.
- Monitoring market prices to identify pricing trends
- Energy supply contracts have a direct impact on costs and CO2 emissions. Therefore, it is important to define:
- Managing projects to reduce water and energy consumption:
- Projects can be of several types:
- Projects requiring complex work with the involvement of external companies.
- Projects requiring simple tasks. Some factories can carry out these projects internally (installing a variable speed drive, a metering instrument, etc.).
- Projects focused on optimizing controls with modifications to setpoints or the implementation of more sophisticated automation.
- Behavioral projects requiring a change in operators’ handling of equipment or production lines.
- Monitoring maintenance operations is also important for maintaining equipment performance over time.
The Energy Management System (EMS)
Having an Energy Management approach is a great start, but to truly maximize benefits and achieve sustainable energy performance, it is relevant to implement an Energy Management System (EMS) compliant with the ISO 50001 standard. This standard provides a structured framework to help organizations integrate energy efficiency into their management practices, whether or not they opt for official certification. The ISO 50001-type EMS is based on several key elements:
4o mini
- Energy policy:
The first step in implementing an EMS is defining a clear energy policy. This policy should reflect the management’s commitment to continuously improving the organization’s energy performance. It must include general objectives and be aligned with the company’s other policies, such as those related to social and environmental responsibility.
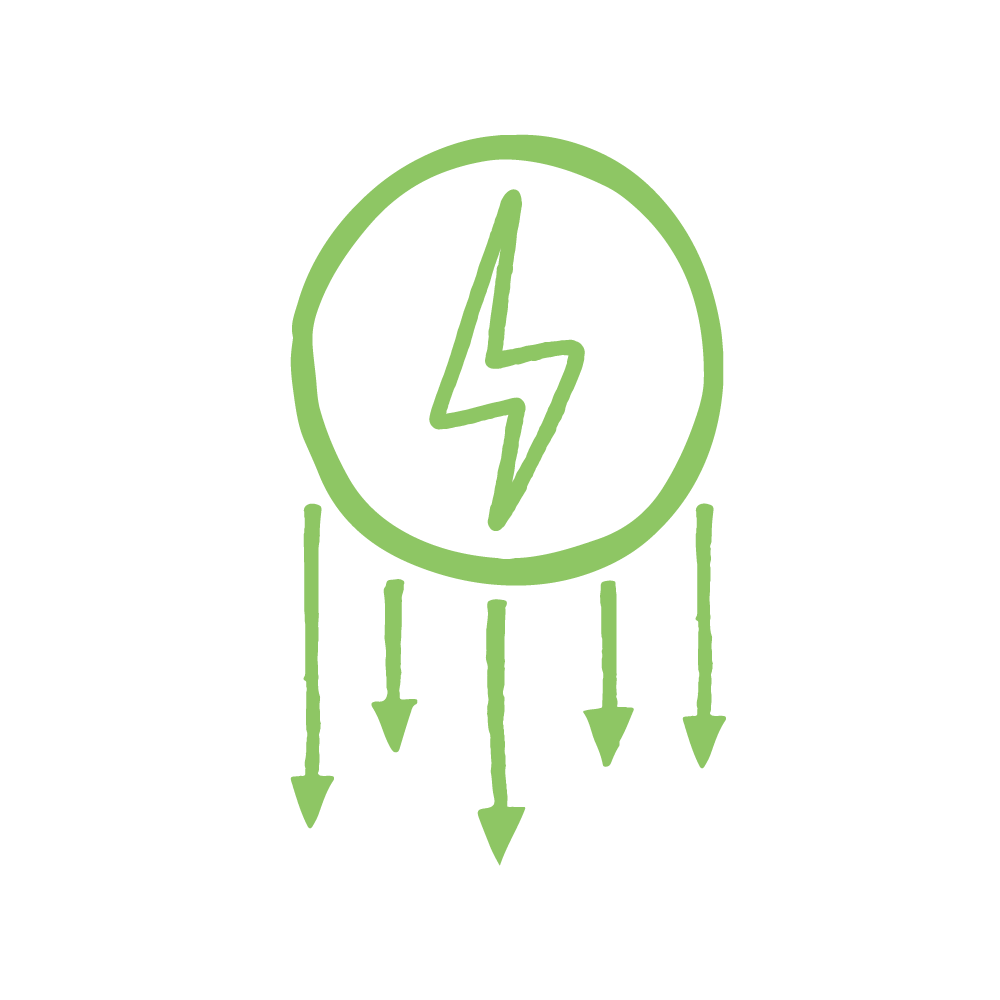
- Energy resources team:
To ensure the proper functioning of the EMS, it is essential to form a dedicated energy management team. This team should consist of members with technical expertise, project management skills, as well as a deep understanding of the organization’s processes.
Energy monitoring and energy audits should help set achievable performance targets for each KPI, with a detailed action plan based on available resources (budget, time, etc.).
- Monitoring and continuous improvement:
Once the EMS is implemented, the energy team must establish template documents and team routines to maintain constant monitoring of energy performance. This includes regularly tracking KPIs, proactively detecting anomalies in water and energy consumption, effectively deploying the developed action plan, and systematically verifying the achievement of set objectives. In case of non-compliance or insufficient performance, corrective actions must be quickly implemented to address the identified anomalies. This monitoring and adjustment process ensures continuous improvement of the organization’s energy performance.
- Annual review and adjustment of the action plan:
Each year, a review meeting is organized to evaluate the deployment of the energy action plan and the performance achieved. This meeting allows for verifying whether the objectives have been met, analyzing the management of detected anomalies to ensure that they have all been properly addressed or closed, and defining a new action plan with updated targets. This process also includes the update of the overall master plan for the factory or the sobriety plan, ensuring that the long-term energy strategy remains aligned with the organization’s goals.
For the effective operation of an EMS within a plant or organization, it is essential to establish training and awareness plans for the teams regarding the Energy Management strategy. Internal and external reporting are also effective ways to highlight developments and engage all collaborators in a virtuous company project!
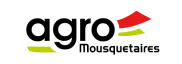
Case study: Dametis supports the Agromousquetaires group at various sites, such as the Laiterie Saint-Père (LSP). In terms of results, the on-site support helped save over the course of a year:
- The equivalent of 120 tons of CO2.
- €120,000 in energy expenses.
Energy Management at the group level
It is essential for each industrial site to implement an energy management approach (EMS) to improve its energy performance. However, for an industrial group with multiple sites, it is crucial to adopt a centralized approach to avoid fragmented efforts and maximize synergies between sites. Unlike the local approach to energy management, energy management at the group level focuses on the coherence of actions and strategic alignment. Here are the key actions to be taken:
- Definición de los Indicadores de Rendimiento Energético (IPE) para la elaboración de informes y benchmarks: Utilities such as water and energy, as well as industrial processes, are often similar within a group. However, different KPIs are frequently observed across sites. By standardizing the KPIs at the group level, it becomes possible to structure reporting coherently, facilitating comparisons and benchmarks. This standardization allows for easier identification of performance gaps and the deployment of effective corrective actions.
- Methodological framework for site energy management: To facilitate energy management at the group level, it is relevant to adopt a unified methodology for all sites. This includes the use of routines, tools, and standard documents. A unified approach not only simplifies management but also helps create a common energy culture, accelerates the adoption of best practices, and ensures continuous improvement of energy performance across all sites.
- Establishment of Technological Guidelines: Factories are often faced with technical recommendations from local actors, which can lead to heterogeneous and sometimes biased technological choices. By establishing technological guidelines at the group level, these risks are minimized by ensuring consistency in the equipment and solutions implemented. This technical coherence promotes better control of installations, simplifies the technical management of factories, and strengthens the overall energy performance of the group.
- Technological monitoring to stay at the forefront of best practices: Technology is evolving rapidly, and it is crucial for an industrial group to stay informed about innovations and best practices in energy management. Continuous technological monitoring helps detect new energy optimization opportunities and integrate emerging technologies quickly across the group’s sites.
- Challenging the action plans of the sites and consolidating a global action plan: To ensure that local initiatives align with the group’s global strategy, it is necessary to regularly challenge the action plans of the sites. This approach ensures that the actions taken are in line with the group’s decarbonization roadmap. Consolidating local action plans into a global plan guarantees a harmonized approach, with clear and measurable objectives at the group level.
- Facilitating workgroups and sharing best practices: Connecting energy teams from different factories is crucial for creating a knowledge-sharing dynamic. Organizing workgroups not only helps disseminate best practices but also creates tailored technical resources, thereby enhancing the skills of teams at each site. This facilitation fosters a culture of collaboration and continuous improvement within the group, which is essential for achieving ambitious energy goals.
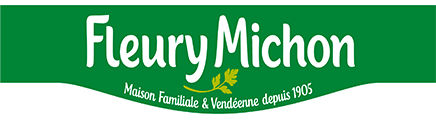
Concrete Example: Dametis also supports Fleury Michon in its group-level Energy Management.
Here are the actions implemented:
- Modeling (digital twins) of equipment (utilities and processes).
- Monitoring of energy performance KPIs
- Categorization of sites
- Comparison of different sites with similar production
- Monitoring of action plans to advise on prioritization
- Monitoring site developments
Implementation of an EMOS
In industry, implementing an effective energy management system is a complex and time-consuming task. To simplify and optimize this process, many industrial companies turn to specialized software solutions. While an EMS (Energy Management Software) allows for tracking energy consumption, reporting on KPIs, and performing basic analyses, it is often limited to these functions. On the other hand, EMOS (Energy Management and Optimization Software) goes well beyond simple reporting.
An EMOS is a powerful and comprehensive tool that unites the operational needs of all departments within the company concerning water and energy management. It offers an extensive range of specific functionalities, such as advanced modeling of equipment on an industrial site, energy purchasing, demand response, cost accounting, and collaborative applications for team-based work. Unlike an EMS, which primarily focuses on data visualization, the EMOS integrates advanced analytical tools that not only detect anomalies but also propose optimized solutions to achieve the best possible energy and environmental performance. Additionally, the EMOS standardizes indicators and work methodologies from one site to another, thus facilitating collaborative management aligned with a global decarbonization strategy.
Ultimately, effective energy management at the site level requires the implementation of an EMOS software. This tool does more than just collect and present data; it also provides integrated expertise and practical solutions to simplify energy management, enable informed decision-making, and facilitate the implementation of corrective actions in compliance with ISO 50001 standards.