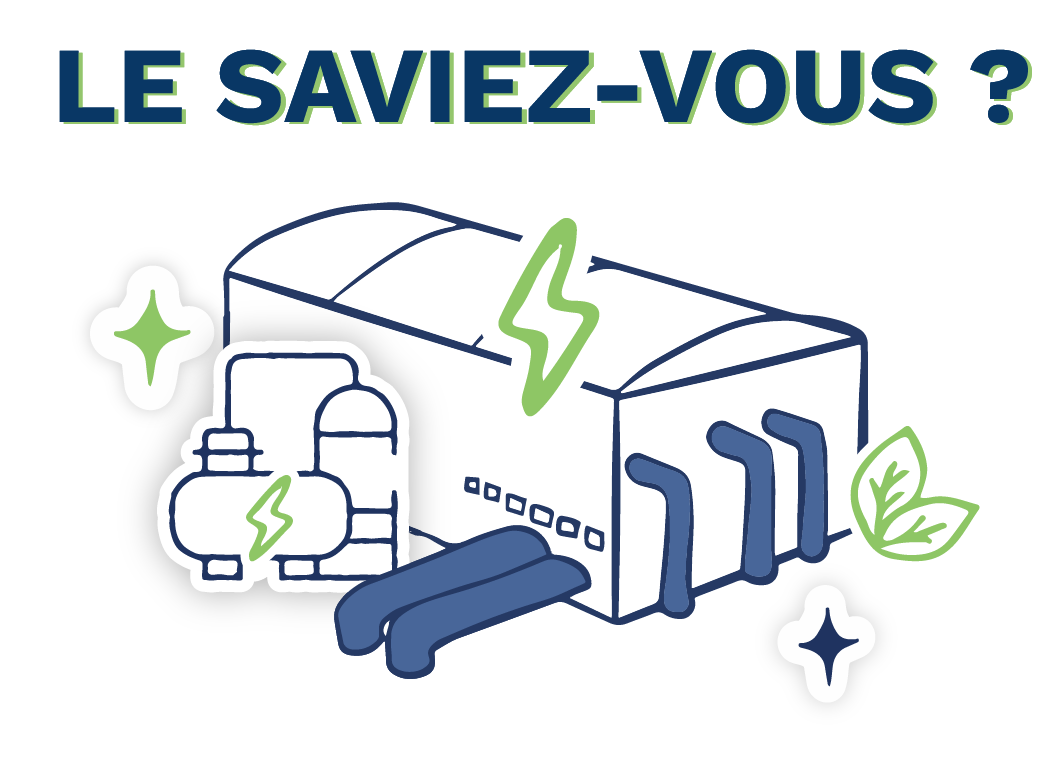
Electrification of processes: an effective lever for decarbonizing industry
Summary
1. Electrify to accelerate the decarbonization of industry
2. Which industrial processes could be easily electrified?
3. What are the technical solutions available for the decarbonization of industry?
4. What are the benefits of process electrification?
5. What other long-term solutions are there for the decarbonization of industry?
Electrify to accelerate the decarbonization of industry
The French energy and climate strategy is clear: achieving decarbonization goals will – alongside massive efforts to reduce energy consumption – involve increasing electrification of uses.
The idea is simple: substitute the combustion of fossil fuels (such as natural gas) with electricity. This strategy includes a prerequisite: the electricity must be decarbonized. Good news, in France, this is already largely the case. According to RTE, the share of decarbonized electricity reached 92.2% in 2023.
Transport, buildings, hydrogen production…many sectors offer electrification potential. And of course, some industrial processes.
56%
The share of electricity in final energy consumption projected for 2050 (versus 27% in 2021).
Source: Ministry of Ecological Transition
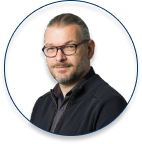
Which processes are concerned? How to electrify? What technical levers to use? For what benefits?
Insights from our expert Sébastien Papouin, Technical Energy Director.
Which industrial processes could be easily electrified?
Two major types of processes are directly affected and could enable the decarbonization of industry:
- industrial activities using furnaces powered by natural gas
- processes with hot water and/or steam needs
There are numerous use cases, whether for hot water at 55-60°C for washing, for cooking at 75-85°C for milk pasteurization, or for steam needs at 7-8 bars.
What are the deployable technical solutions for the decarbonization of industry?
Industrial Furnaces
To follow our typology, furnaces powered by natural gas can be replaced by electric furnaces.
This is currently seen in heavy industry such as steelmaking with the use of electric arc furnaces instead of fusion furnaces. Examples are also found in the glass industry.
But replacing gas-powered furnaces with electric ones is also possible – and easier to implement – in other fields, particularly for cooking uses.
Note, evolving the process to electricity requires anticipating the increase in necessary electrical power across the entire site, as well as the associated equipment (transformers, electrical cabinets, etc.).
Hot Water
The production of hot water and steam is also well-suited to process electrification, with various technical solutions.
First, it’s possible to replace the gas boiler with resistive heating, that is, an electric boiler to produce hot water or steam. This is feasible for low power.
Next, a gas boiler can be replaced by a heat pump (HP) which benefits from a high performance coefficient. Currently, catalog HPs can produce hot water up to about 100°C.
The most interesting scenario involves utilizing a waste heat source from the process to supply the HP (which will raise the temperature to the useful level). Some agri-food activities are particularly well-suited for this, such as refrigeration production.
High and Low-Pressure Steam
To produce higher pressure steam, there are also custom, non-standardized HPs, which can directly produce steam at 7 bars (around 170°C) for example. The HP then becomes the process steam boiler.
For industrial activities without a waste heat source to utilize, solutions also exist. It is possible to draw heat from the ambient air. To reach the useful temperature, it is necessary to install HPs in series, which increases the investment cost.
Another example in the world of liquid concentration with evaporators. The driving force of steam is replaced by MVR (mechanical vapor recompression) or TVR (thermal vapor recompression), which increases the pressure, thus the temperature, of the vapor from the water evaporation of the liquid to be concentrated.
Heating/Drying
Another electrification of processes is heating and/or drying by radiation with infrared, microwaves, high frequencies. Technologies applicable depending on the shape and type of product (wave/product interaction).
What are the benefits of process electrification?
The substitution of natural gas with electricity in France provides considerable gains in reducing CO2 emissions related to the process.
For example, based on the carbon content of electricity in 2023, it is estimated that electrifying processes will lead to a sixfold reduction in CO2 emissions, which is promising news for the decarbonization of industry.
But process electrification can also bring financial gains as shown in the customer case study below:
32 g CO2/kWh
The carbon intensity of electricity production in France in 2023 (compared to more than 200 g CO2/kWh for natural gas combustion)
Source: RTE
Customer case study:
- Initial process: gas boiler for hot water production at 90°C
- Power: 900 kW of heat
- Technical solution: replacement of the boiler by series HPs (cold source: ambient air)
→ Annual OPEX savings: €75,000
Source: Dametis
What other long-term solutions are there for the decarbonization of industry?
Replacing fossil fuels with hydrogen is also a solution. It could be said that this is an indirect electrification of processes. Indeed, to achieve industrial decarbonization goals, the hydrogen used must itself be decarbonized. Therefore, it must not be produced from fossil fuels (such as natural gas steam reforming), as is mostly the case worldwide currently, but by electrolysis, with the electrolyzers themselves powered by decarbonized electricity. This solution is technically viable, but the market is still emerging, and currently, there is a limited availability of green hydrogen.
Blog
Discover our latest articles
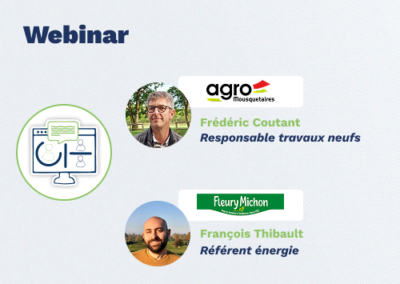
Webinar #5: How Etria optimizes its energy usage, reduces costs, and calculates the carbon footprint of its finished products
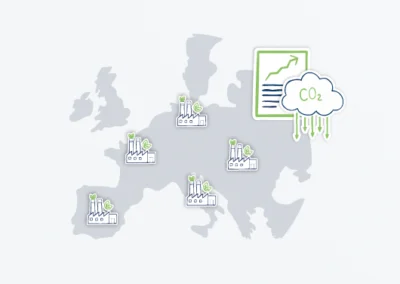