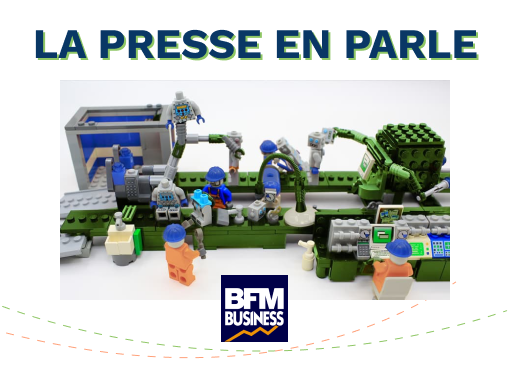
BFMTV talks about us: “Dametis, Decarbonizing the Manufacturing Industry”
In this article, we will explore the key points highlighted by BFMTV and emphasize why Dametis is at the forefront of industry decarbonization.
Unique Predictive Tool and Expert Team for Decarbonizing Industry
At Dametis, we distinguish ourselves with our approach that combines the use of a unique predictive tool “MyDametis” and a highly qualified team of experts to help industries reduce their energy consumption, control their carbon footprint, and optimize their decarbonization processes.
MyDametis relies on advanced algorithms and statistical models to analyze and understand the various variables impacting industrial energy consumption, water usage, and material loss in industrial processes.
It collects real-time data from sensors, equipment, and control systems, then analyzes them to detect inefficiencies and identify optimization opportunities for decarbonizing the industry.
We are actively able to help industries reduce their carbon footprint by proactively identifying specific actions that optimize their processes and minimize greenhouse gas emissions. Our approach goes beyond mere carbon offsetting, preferring concrete measures to directly reduce emissions at the source.
Imagine having specialists working 24/7 to optimize your industrial sites. That’s what MyDametis offers you, the only platform designed 100% by experts in environmental performance.
However, at Dametis, we also understand that technology alone is not enough.
That’s why we have assembled a team of experts composed of energy specialists, water specialists, engineers, and other experienced professionals. These experts work closely with our clients to understand their specific needs, evaluate their installations, interpret the results provided by MyDametis, and propose tailored solutions.
By combining our predictive tool MyDametis and our expert team, Dametis offers a comprehensive approach to help industries achieve their decarbonization goals and accelerate their environmental transition.
Digital Twins for Optimized Performance
Digital twins are based on the Lego theory, where each factory is considered a unique construction made up of similar bricks. They are used to analyze the various stages of the industrial process, identify weaknesses, and propose specific improvements.
- Exact Reproduction of the Factory: This first digital twin is an accurate reproduction of the actual factory. It is used to diagnose drifts and inefficiencies. By comparing actual performance with this model, we can identify gaps and optimization opportunities.
- Imitation of Factory’s Usual Operation: This second digital twin simulates the normal operation of the factory, analyzing drifts brick by brick. This allows identifying areas where specific improvements can be made to optimize performance.
- Peak Performance of Each Block: The third digital twin represents each individual block of the factory at its optimal performance level. It helps determine the best performance already achieved by each brick, thus setting clear improvement goals.
- Use of the Most Advanced Technology: The fourth digital twin models each block with equipment replaced by the most advanced existing technology. This allows visualizing the potential impact of adopting cutting-edge technologies on overall factory performance.
- Most Optimal Digital Twin: The fifth digital twin represents the factory with the best possible configuration, where each brick is equipped with the most advanced technology and the configuration is optimized for maximum performance. This model serves as the target to be achieved during our interventions.
Thanks to these different digital twins, Dametis is able to thoroughly analyze every aspect of the factory, identify optimization opportunities, and recommend specific measures to improve energy efficiency, water management, and material loss reduction.