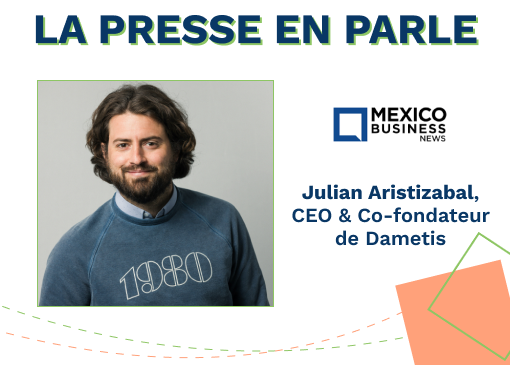
Achieving the ideal industrial plant with industrial data analysis
Interview by Julian Aristizabal, CEO and Co-founder of Dametis, in Mexico Business News.
What has been the company’s trajectory in the Latin American market?
Which sectors would benefit most from your product?
Dametis works with what we call traditional industries, such as food and beverage, cosmetics, pharmaceuticals, electronics, automotive and many others. In fact, Dametis works with all industrial plants that have conventional utilities such as compressed air, chilled water and steam, among others. These are industries with which the company knows how to work and has a wealth of experience to bring added value. For example, we work with Renault to help them optimize their painting process, or with the major dairy industry.
How did you adopt Lego theory in your analysis, and how does it benefit different types of installation?
The Lego theory is the fruit of the experience of Dametis engineers. People founded the company with decades of experience. These experts have a work methodology that they reproduce in each plant. It’s often said that no two factories in the world are alike, but they’re all made up of the same components. For example, an air compressor is the same in plant A as in plant B.
So we began to wonder whether our methodology could be implemented and carried out by software. An engineer can analyze a few plants a year, but software has no limits. To do this, we had to create a frame of reference to model a plant and integrate our analysis algorithms.
What are the main improvements you’ve seen since implementing your solution?
The software first evaluates three categories in percentage terms.
– The first is what we call the ideal plant: a plant which, because of its technical and production characteristics, can consume as little energy and water as possible. This would give the plant a 100% rating.
– The second rating would correspond to the best plant performance with optimized regulations and no additional investment.
– The third score corresponds to the plant’s actual performance in real time.
The software creates this reference point for each block or piece of equipment in the plant. In this sense, we achieve rapid gains in the management and visibility of technological solutions that could be applied to achieve the goal of the ideal factory.
Imagine having specialists working 24/7 to optimize your industrial sites. That’s what MyDametis offers you, the only platform designed 100% by experts in environmental performance.
What basic recommendations would you give to players in the energy, oil and gas industry who are working on their green transition?
What is the estimated return on investment for Dametis’s projects?
The energy management software itself allows for better management and understanding of plants. Thus, without additional investments, the software can generate average savings of 5% on energy and water consumption. Nevertheless, the projects that result from the use of the software can be even more compelling. We have optimized systems and achieved up to 20% savings through smart regulation.